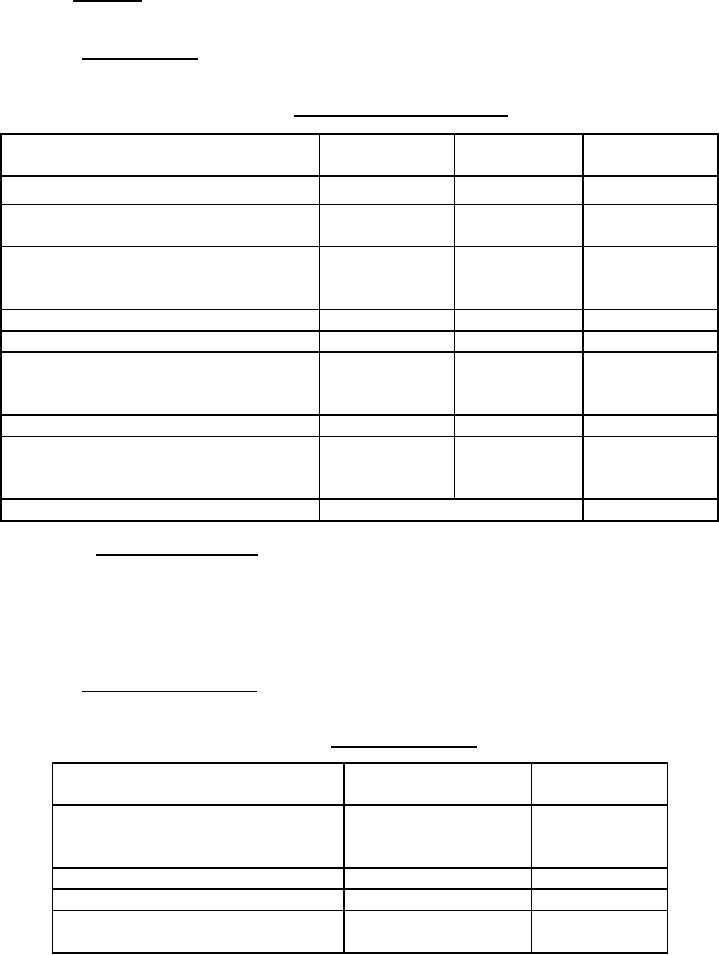
MIL-DTL-29597C(NAVY)
3.2 Materials. Odor barrier bags shall be made from such materials and processes as to
ensure compliance with the requirements of this specification.
3.2.1 Barrier material. Barrier material shall meet all of the performance requirements in
table I and 3.2.1.1 of this specification.
TABLE I. Barrier material requirements
TEST
PROPERTY
TYPE I
TYPE II
REFERENCE
Thickness, inches (max)
0.010
0.010
4.4.1
Water vapor transmission rate,
6.0
6.0
4.4.2
grams/square meter/day (max)
Oxygen transmission rate,
cubic centimeters/square meter/day
1.0
1.0
4.4.2
(max)
Tensile breaking factor, lbs/inch (min)
20
45
4.4.3
Elongation, percent (min)
400
500
4.4.3
Tear strength
Peak load, lbs (min)
8.0
31
4.4.4
Energy to break, in-lbs (min)
15.0
80
Puncture resistance, lbs (min)
9.0
19
4.4.5
Heat seal strength
Breaking strength, lbs/inch (min)
12
24
4.4.6
Energy to break, in-lbs/inch (min)
16
77
Odor barrier effectiveness
Rating of 1 or less
4.4.11
3.2.1.1 Material compatibility. After the fluid immersion conditioning specified in 4.4.12,
the barrier materials shall be tested for Tensile Breaking Factor, Elongation and Tear Strength
properties. The test requirements after immersion shall be as follows:
a. Type I: 50% of the obtained test values of 4.4.3 and 4.4.4.
b. Type II: 75% of the obtained test values of 4.4.3 and 4.4.4.
3.2.2 Adhesive (class 1 only) . The adhesive used in type I bags shall be acrylic with no
fibers or carrier within the adhesive and shall meet all the requirements in table II.
TABLE II. Adhesive properties
TEST
PROPERTY
CLASS 1
REFERENCE
Adhesive seal strength
4.4.7
Initial seal strength, oz/inch (min)
48
Re-seal strength, oz/inch (min)
35
Adhesive seal integrity
No leakage
4.4.8
Relaxation modulus ratio
0.066 to 0.160
4.4.9
Adhesive areal weight,
29 to 35
4.4.10
grains/24 square inches (min)
4
For Parts Inquires submit RFQ to Parts Hangar, Inc.
© Copyright 2015 Integrated Publishing, Inc.
A Service Disabled Veteran Owned Small Business